Stage Collars
Composite - Type 778MC
Continuing our commitment to innovation, Forum’s new Davis-Lynch™ Composite Stage Collar offers improved drill-out performance and superior sealing capabilities for 2 or 3-stage cementing solutions. Utilizing the proven design of our mechanical stage collars, our Composite Stage Collar is a highly-reliable stage tool featuring a high-strength composite opening seat and improved drillability.
Forum Composite Stage Cementing Collar features include:
- Proven stage collar design Davis-Lynch™ has been running since 1993, with new high-strength composite opening seat comprised of material identical to that used in Forum Frac Plugs.
- Over 10% decrease in drill-out time on average.
- Composite opening seat locks against-rotation during drill-out.
- No continuous composite rings left after drill-out to hang up on PDC drill bits.
- Convolute-Tube composite material maximizes burst, collapse and shear strength.
- No continuous filament-wound material in opening seat or opening device, that hinders the PDC bit penetration rate.
- Dimensionally stable composite material with maximum temperature rating to 350°F.
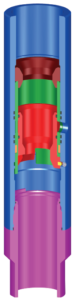
Mechanical - Type 778MC
While now established as a field proven tool, this tool continues to be the subject of research and development to find new materials for faster drill-out time, greater PDC bit drillability and better metal-to- metal sealing. Features of the 778 MC Stage Cementing Collar include:
- Tools can be made from material grades up to 150,000 psi minimum yield, including material suitable for sour gas service.
- All parts are custom fitted and subjected to extensive quality control standards for maximum performance downhole.
- The connection that adjoins the stage collar body and the bottom sub affects a metal-to-metal seal and engages a back-up elastomer seal, the two of which are designed to provide gas-tight pressure integrity.
- No welds are used on any portion of the tool.
- The reduced length of the tool minimizes the effect of bending stresses.
- The seals providing internal and external pressure integrity are housed in the stage collar body and remain stationary throughout operation, minimizing chances of their being damaged.
- The pressure-relief design prevents fluid trapping and compression between the opening device and the closing plug during the closing phase of the tool’s operation.
- The closing sleeve is held in the closed position by an internal lock ring.
- Both the opening and closing sleeves lock against rotation for easy drill-out.
- A minimum amount of aluminum and rubber are the only materials encountered during drill-out. Plug sets for four different cementing applications are available.
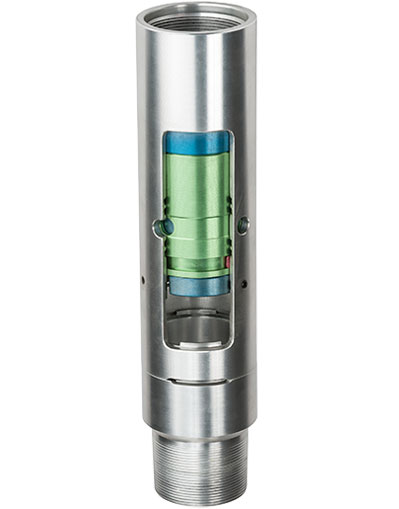
Hydraulic - Type 777HY
This stage collar features an opening sleeve with area differences on opposite ends that allows it to be manipulated hydraulically. The closing sleeve is identical to the one contained in the Type 778 MC Mechanical Stage Cementing Collar. The development and introduction of this model was spurred on by the tremendous upswing in horizontal drilling activity that has occurred in recent years. The hydraulic opening feature makes this tool’s use very practical in horizontal wells.
The elimination of the need to use a mechanical opening device has several other merits. Casing runs in highly deviated wells can now be two-stage cemented without having to use continuous displacement type plugs. In certain applications, liners run with drill pipe can be run in conjunction with one or several inflatable packers and used to isolate and selectively cement certain casing intervals. Slotted or pre-drilled liner can be run below a Forum inflatable packer/hydraulic stage collar assembly, allowing cement to be pumped above the packer and isolated from highly sensitive producing zones.
Along with all the features inherent in the 778 MC Stage Cementing Collar, the Type 777 HY offers:
- Effective differential area on the opening sleeve that generates a high opening force while requiring only optimal pressure to do so.
- The ability to open immediately upon the completion of first-stage cement displacement.
- Opening pressure values that can be adjusted at the time of assembly to assure that all inflatable packers or other hydraulic tools present in the casing string will be triggered at the correct juncture.
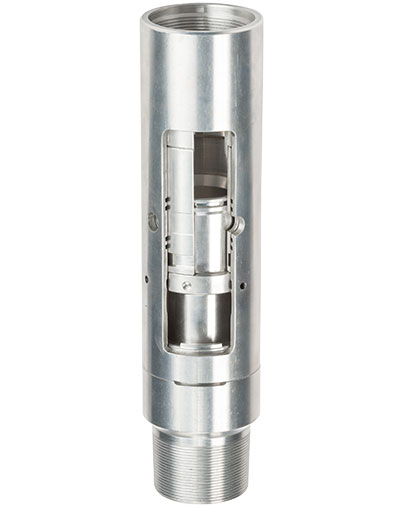
Packer Stage Collar
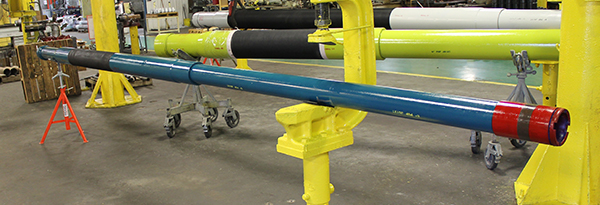
Forum Energy Technologies’ Davis-Lynch packer stage cementing collar (PSC) helps ensure proper placement of competent cement in the intermediate casing string, while expanding the operating envelope. By combining an inflatable packer and a stage cementing collar, the PSC reduces NPT and well construction costs, while complying with regulatory requirements and minimizing HSE risks.
Reduce Costs
Through packer stage collar or PSC, our clients are able to reduce their construction and NPT costs. On top of cutting costs, PSC also allows you to mitigate HSE risks and comply with standard regulatory requirements. With a packer stage cementing collar, you can ensure cement keeps falling around slotted or pre-drilled liners.
Isolate Zones
PSC can also help you isolate the second stage cement hydrostatic head from the first cement stage. Similarly, you can isolate from pressurized zones and choose a cement placement across interested zones. Through packer stage collar, you can avoid gas migration that might impact primary cement-based jobs and create annular gas issues on the surface.
PSC: One Tool, Diverse Use Cases
The use cases of the packer stage collar are diverse but it serves as a singular tool. For instance, one person can service a PSC and cut out the added costs of another person who would have to purchase a stage collar and inflatable packer from two different companies.
Mechanics of Packer Stage Collar
PSC tool comes with an inner tube that is protected through mechanically end-anchored and spring steel reinforced strips. Both are encased in an outer oil-resistance rubber. The expansion comes into play when you inject fluid straight into the inner tube.
As a result, the injection leads to partial unleafing of all steel strips that stretches to the outer rubber. This, in turn, has a direct impact on a full-length seal which is either cased or has an open hole. In layman’s terms, once the packer continues to expand, the element’s bottom end stretches on top of a ratchet-style mechanism. It is an added feature of the element that mechanically expands in order to provide full support in the event of a hydraulic failure.
Extended Benefits of Packer Stage Collar
Reduces HSE Risk
Another benefit of the packer stage collar is that it reduces and mitigates HSE risk related to trouble zones and misplaced cement jobs.
Zone Isolation
One of the perks of using a packer stage collar is that it allows zonal isolation. It means you can work out trouble zones with just one simple tool.
Reduce Potential Chances of Remedial Cementing
With a packer stage collar, you can minimize the chances of remedial squeeze cementing. You can also cut out the need to enhance cementing plug in the first stage.
Eliminate Flat Time
One of the most advantageous aspects of using the packer stage collar tool is that it cuts out flat time.
Features of Packer Stage Collar
PSC comes with added features that make it more appealing to a diverse range of clients. Packer stage collar runs in a specific sequence, can pump cement for second-stage in an instant, is compatible with water and oil muds, combines two dedicated tools into a single solution, and supports plugs for the first and second stage.
Contact us to learn more about packer stage collar.
PSC-M
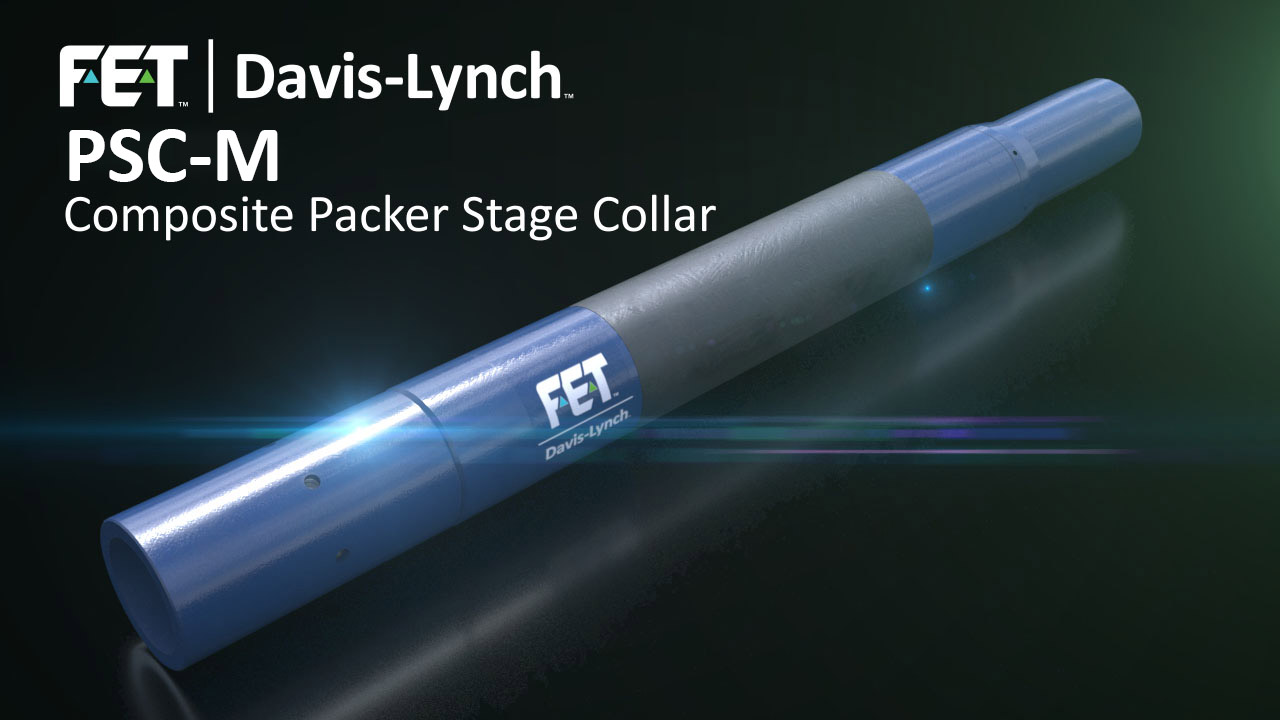
The FET Davis-Lynch PSC-M Composite Packer Stage Collar is a combination of the 778-MCCS Composite Stage Cementing Collar mated to the Type 100 Integral Casing Packer. This allows for all the benefits of continuous tool operations from a stage cementer mated to an integral inflatable casing packer to form a Packer Stage Collar with combined efficiencies of the faster drill-out times of a composite seat multiple stage cementing tool.
Key Benefits
- Faster drill out times
- Minimal amount of composite and rubber material to drill out
- Less wear on PDC bits during drill out
- Enhanced tool operating control from only a 1-piece tool
Features
- Built in Texas with API-Q1 manufacturing practices
- Opening and closing sleeves with locking and non-rotating drill out features
- Available in most casing grades and threads to match customer wellbore designs
- Rated for operating temperatures to 275° and up to 375° with use of special seals
- Composite seat material temperature stable to 350°
- Manufactured with selectable opening and closing sleeve operating pressures
- Various operating plug set options available
- Can be placed in wellbores with up to 30° well deviation
- Patented Inflatagrip non-welded reinforced inflatable element
- Stationary internal seal design for reliable sealing
- No filament wound type materials used in the composite sleeve construction
- Inflatable element and stage tool seals are factory pressure tested prior to field deployment
- Fully Reinforced inflatable rubber element with locking feature during expansion
- Reliable valving mechanism to ensure proper inflation and closing