Summary
Forum Energy Technologies partnered with a major O&G operator in the Permian Basin to provide technology which eliminate ESP failures as well as issues with efficiency caused by sand fallback. This study is ongoing, and already several of the ESPs have had their run life increased by as much as 800%, resulting in a potential cost savings of millions of dollars.
Background
An ESP (electrical submersible pump) is commonly placed 8,000 feet or more below surface. Sand is one of the major issues that leads to ESP failure, wear and loss of efficiency. Improvements in handling sand and de-sander technologies help, but are often not enough to keep the system running efficiently. Restarts are an especially high-risk event for ESPs. That risk is amplified when sand is present in the production fluid.
What is sand fallback and how does it cause ESP wear/failures?
There are a number of reasons why an ESP will shut down. Common causes are inconsistent power, surges in power, and gas slugging. It can also be caused by pre-set shut down parameters that shut down ESP operations for self-preservation when key operational parameters are outside the safe running zone. When oil is produced from a reservoir, the production fluid often contains large amounts of sand, water and gas. After shutdown, all solids within the thousands of feet of production fluid in the tubing above the ESP will fall and come to rest on top of the system. This results in multiple tubing joints full of sand settling directly on top of the ESP internal components. When an ESP is restarted with large amounts of sand resting above it, a hard start/rock start occurs. Hard starts are the best-case scenario in this situation, but these types of starts increase wear and damage the ESP. Over time, the hard starts will make the ESP less efficient and shorten its run life. Often this best-case scenario does not happen and a catastrophic failure occurs. Examples of a catastrophic failure due to sand fallback can include a broken shaft or an electrical failure due to high amperage while trying to start the ESP.
Solution
A major oil and gas producer in the Permian basin was facing a series of short ESP runs caused by sand fallback. This led to increased NPT (Non Productive Time), workovers and costly ESP purchases. Forum Energy Technologies approached the customer offering the SandGuard as a solution to eliminate issues related to sand fallback.
The positive results of the implementation of the SandGuard™ result in the elimination of broken shafts, and elimination of electrical failure during restart – all of which result in longer lasting ESPs. This customer has seen significant value added to their operations thanks to the SandGuard™. Before and after data from the ESP wells currently running with SandGuard™ show this solution has saved the customer millions of dollars in both ESP failures and deferred production.
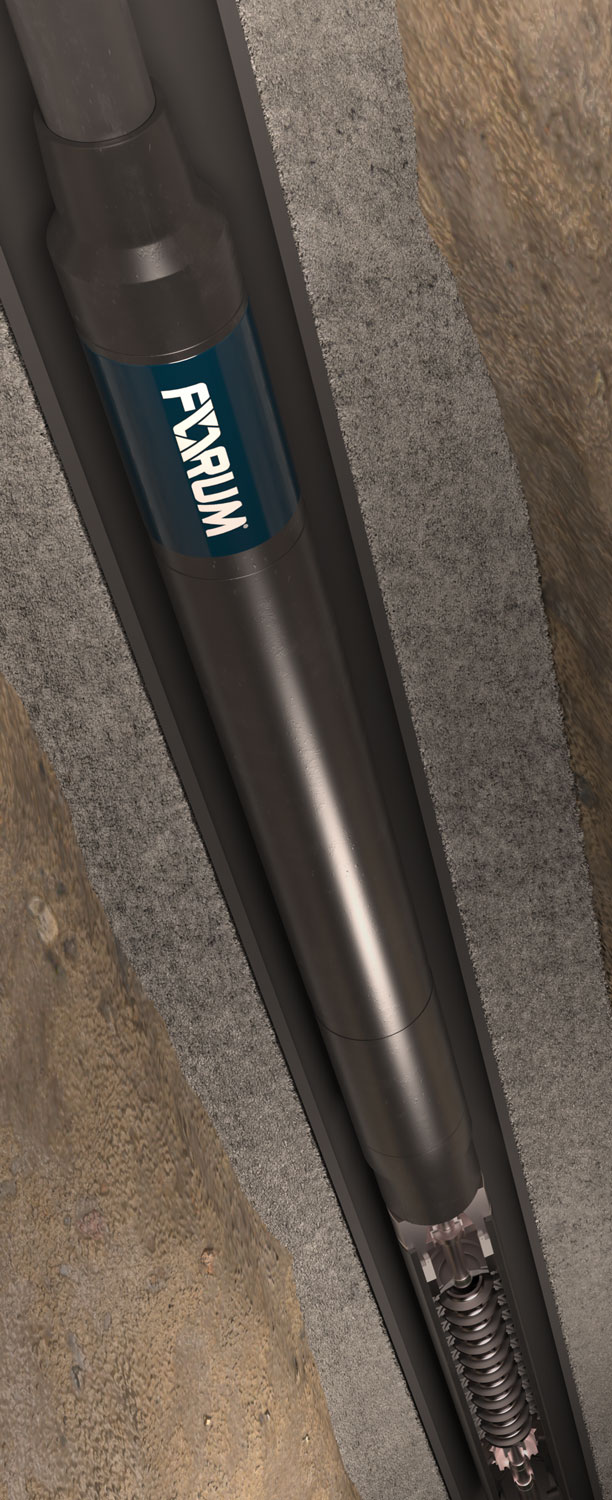
Before SandGuard
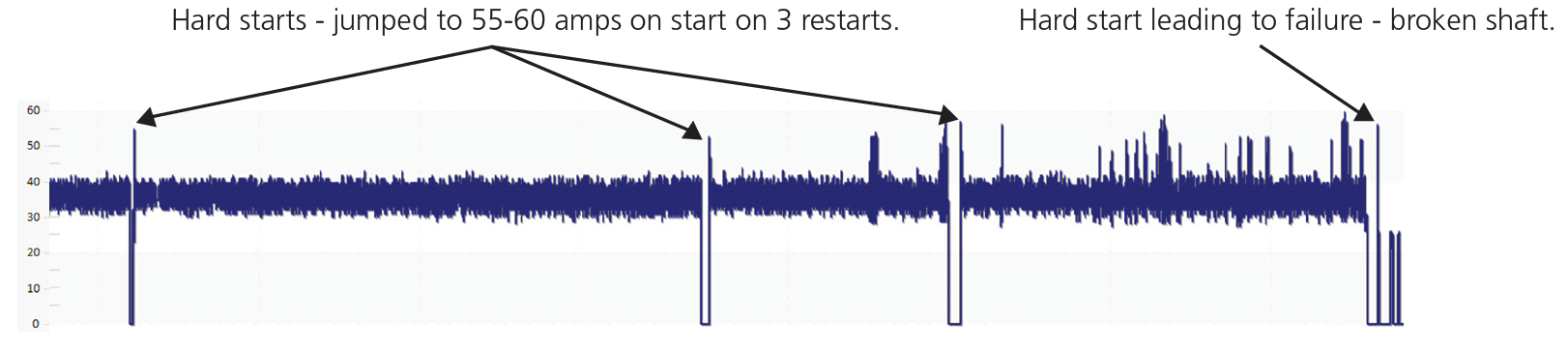
After SandGuard
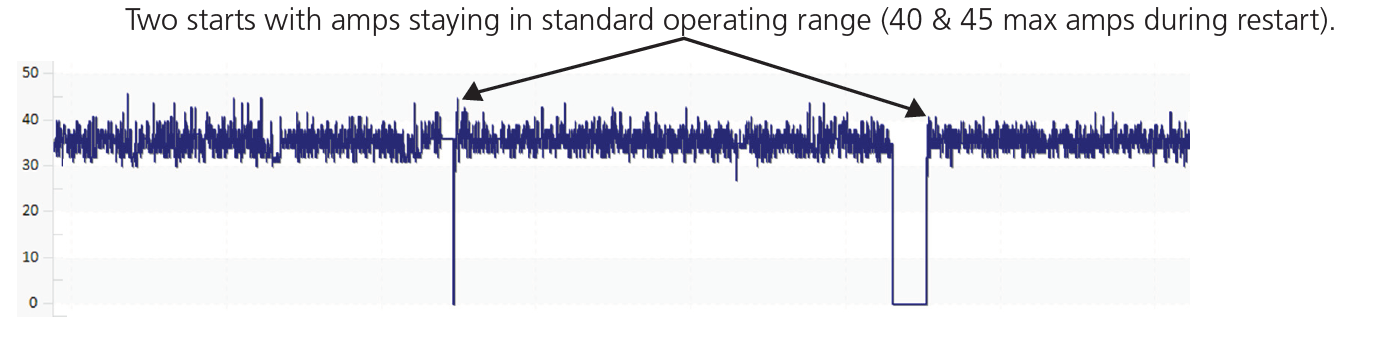
Workover and Deferred Production Cost
New ESP | $150,000 | |
Cost of Rig & Misc. Rig Costs (Pump truck, BOP rental, electrician) | $15,000 | |
Workover Cost | $165,000.00 | |
$/BBL of Oil | $25 | |
Daily Fluid Production | 1500 | |
Oil per BBL | 40% | |
Daily Revenue | $15,000 | |
Deferred Production Days | 9 | |
Total Deferred Production Revenue Per Workover | $135,000.00 | |
Total Cost and Lost Revenue Per Workover | $300,000.00 |
Potential Workover Production Savings Based on Last ESP Run at $300,000 per Workover
Well # | Previous ESP Run Days | Current ESP + SandGuard Run Days (All Still Running) | Savings Based on Previous ESP Run Life | Notes |
1 | 41 | 320 | $2,400,000.00 | 8x previous run (still running) 3 Previous Sand Failures |
2 | 54 | 220 | $1,200,000.00 | 4x previous run (still running) 2 Previous Sand Failures |
3 | 128 | 145 | $300,000.00 | 1 Previous Sand Failure |
4 | 29 | 67 | $600,000.00 | 2x previous run (still running) 1 Previous Sand Failure |