The dead short leak is the only type you can effectively deal with in the field. A good quality ohmmeter (Fluke) that reads to a minimum of 0.1 Ohms is essential in determining if you have a dead short leak. Use the following methodology to test for a dead short:
1) The first step is to short your meter leads and record this resistance reading. Subtract this lead resistance from all resistance measurements to eliminate errors due to the resistance of the leads.
2) Disconnect both cable ends and ensure the leads are clean.
3) Measure the resistance of the conductor to ground (armor) on the whip end Rw.
4) Reverse the leads and again measure Rw. If the resistance significantly differs with the leads switched, you have a wet leak and a precise location in the field is impossible. Proceed to step 7. If the readings are the same, proceed to step 5.
5) Measure the resistance of the conductor to ground (armor) on the drum end Rd.
6) If the leak is not wet, use the formula below to determine if you have a dead short, where Rc is the resistance of the current length of the conductor (from the cable record book).
If the value of Rc in the cable record book is questionable, measure the conductor resistance.
If (Rd + Rw – Rc) < 300 Ω, you have a dead short; otherwise, you have a high resistance leak. If you have a dead short, skip step 7.
7) If there is a high resistance or wet leak, the next step before going to a service center is to unwind several hundred feet of cable and, with the Ohm meter attached at the drum end, watch the Ohm meter as this loose cable flexes along the length by hand. It is a crude but sometimes very effective way of leak location as many cable leaks occur within a few hundred feet of the whip end. After finding the leak, cut the cable and test. If the leak is still present, you must take the cable to a service center.
If the resistance is less than 300 Ω, follow these steps to determine the leak’s location.
1) Find the cable’s total length (L) from the cable record book.
2) Calculate the cable length to the leak from the whip end (Lw) using the following formula:
Lw = (Rc + Rw – Rd) x (L / (2 x Rc))
3) Calculate the cable length to the leak from the drum end (Ld) using the following formula:
Ld = (Rc + Rd – Rw) x (L / (2 x Rc))
This example shows how to use the formulae:
L = 24,500 ft. (7,468 m)
(For metric, use meters in the same formulae)
Rc = 68.6 Ω
Rw = 149.4 Ω
Rd = 205.2 Ω
First, test to see if it is considered a dead short:
(Rd + Rw – Rc) = 286.0 Ω Less than 300 Ω
Check leak distance from the whip end:
Lw = (68.6 + 149.4 – 205.2) x (24,500 / (2 x 68.6)) = 2,286 ft.
Check leak distance from the drum end:
Ld = (68.6 + 205.2 – 149.4) x (24,500 / (2 x 68.6)) = 22,214 ft.
Once you have located the leak, slack the cable, examine it for physical damage, and manually flex it while observing the leakage resistance. You should find variations in the ohmmeter reading if you are at the leak. If the leak is close enough to the whip end that you can spool down and cut off, and you have enough cable remaining to perform the current services, then do so. After cutting out the short, test the remaining cable to ensure electrical integrity. Re-head and finish the job.
If the leak is too far from the whip end to cut out, you must take the cable to a service center for inspection. At a service center, they are well-equipped to deal with all types of leaks. Burning a leak out with a “burn-out” box is the fastest way to identify difficult leaks. The service center will also have more sophisticated equipment than an ohm meter to try and locate the exact point of failure. If the service center suspects the damaged cable is from mechanical damage or temperature, a burn-out box will save time finding the leak. However, if it is essential to determine the cause of the leak, then do not use a burn-out box as it will destroy the area around the leak and likely make it impossible to perform a root cause analysis of the failure.
Note: This picture shows the damage to the conductor and the armor as a result of using a burn-out box.
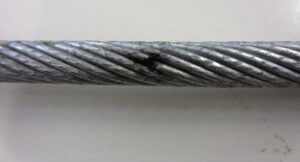